The Chlor-Alkali Industry primarily produces chlorine, sodium hydroxide (caustic soda), soda ash (sodium carbonate), sodium bicarbonate, potassium hydroxide, and potassium carbonate. The materials required are:
1.Brine (Salt Solution)
Source: Sodium chloride (NaCl), which is dissolved in water to create brine.
Uses: Provides the chlorine and sodium ions required for the process.
●
2.Water
Source: Clean and demineralized water.
Uses: Acts as the solvent for dissolving salt and provides hydrogen ions during electrolysis.
●
3.Electricity
Source: Energy supply (often from thermal, hydro, or renewable sources).
Uses: Powers the electrolysis process to split the brine into chlorine gas, hydrogen gas, and sodium hydroxide.
●
4.Membranes/Diaphragms (for Membrane or Diaphragm Cell Process)
Source: Specific synthetic materials (e.g., perfluorosulfonic acid membranes).
Uses: Separates the anode and cathode compartments to prevent mixing of products.
●
5.Anodes and Cathodes
Source: Specially designed materials (e.g., titanium coated with noble metals for anodes and steel for cathodes).
Uses: Electrodes for the electrolysis process.
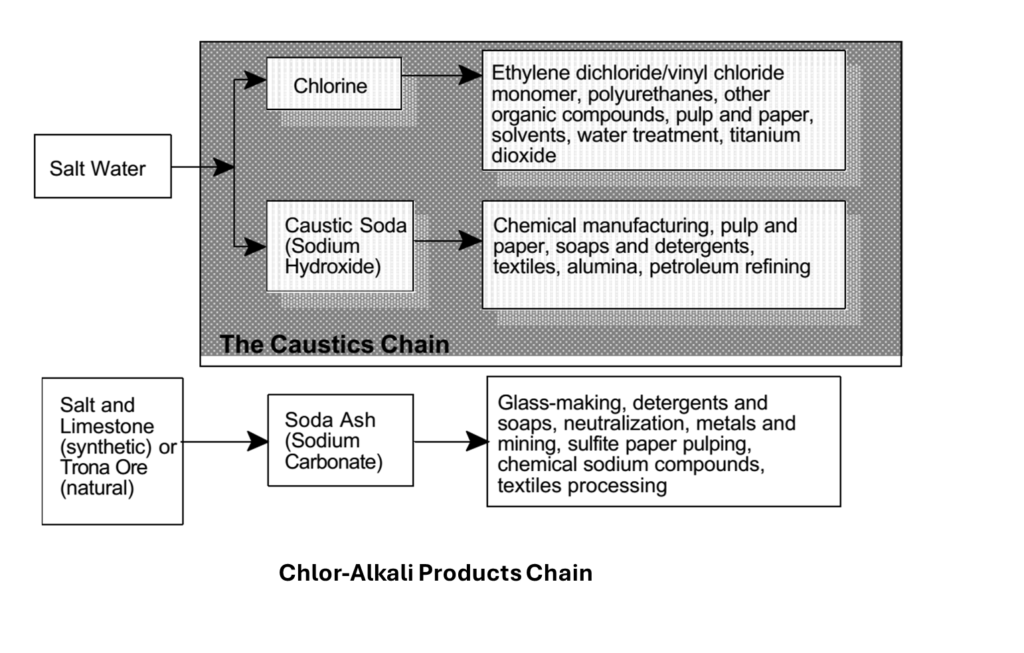
Chlor-Alkali Products Chain
The manufacture of caustic soda (sodium hydroxide, NaOH) is primarily achieved through the electrolysis of brine (sodium chloride solution).
Reaction
2NaCl + 2H2O → Cl2(g) + H2(g) + 2NaOH(aq)
At the Anode (+): Chloride ions from brine are oxidized to produce chlorine gas:
2Cl– → Cl2(g) + 2e–
At the Cathode (-): Water is reduced to produce hydrogen gas and hydroxide ions:
2H2O + 2e– → H2(g) + 2OH–
Products:
Chlorine Gas: Collected at the anode.
Hydrogen Gas: Collected at the cathode.
Sodium Hydroxide: Formed in the solution near the cathode.
The electrolysis of brine process can be carried out using one of three main methods:
1.Membrane Cell Process
2.Diaphragm Cell Process
3.Mercury Cell Process
Membrane Cell Process
Most Modern and Widely Used
Steps:
1.Brine Preparation:
Sodium chloride is dissolved in water and purified to remove impurities like calcium, magnesium, and sulfates.
2.Electrolysis:
●
Brine is fed into a cell with a cation-exchange membrane separating the anode and cathode chambers.
3.Product Recovery:
●
Sodium hydroxide and hydrogen gas are collected in the cathode chamber, while chlorine gas is collected in the anode chamber.
Advantages:
•High purity NaOH.
•Low energy consumption compared to other processes.
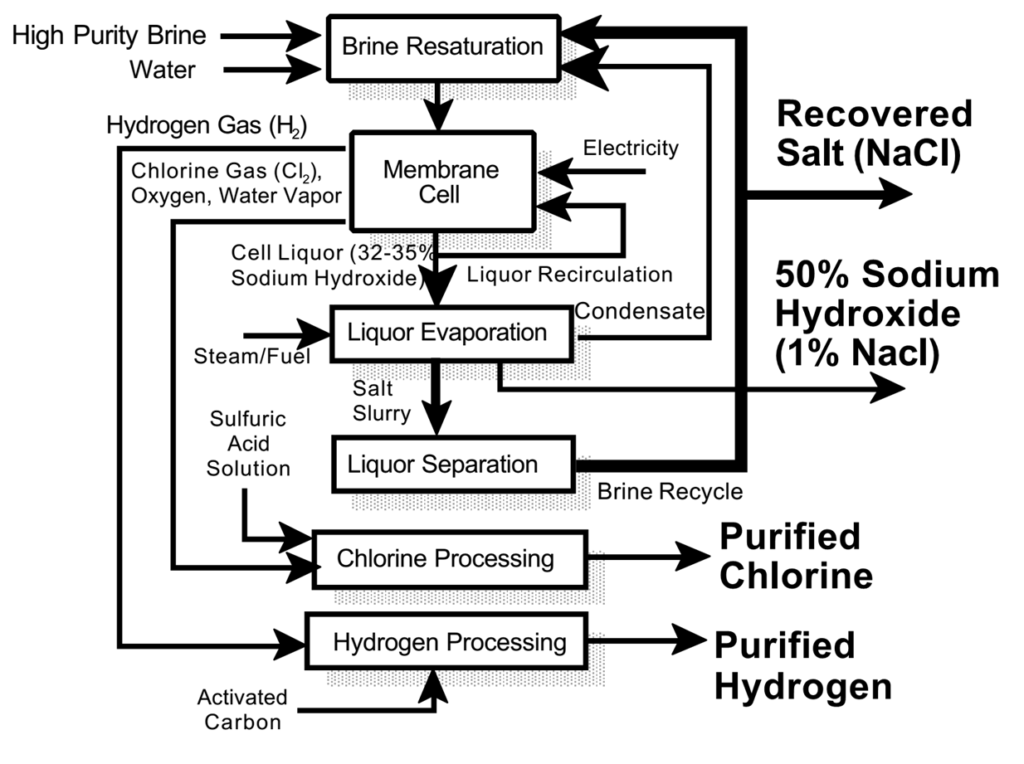
Diaphragm Cell Process
Steps:
1.Brine Preparation:
1.Impurities are removed, but some calcium and magnesium traces can remain.
2.Electrolysis:
1.A porous diaphragm separates the anode and cathode chambers.
2.Reactions are similar to the membrane cell process.
3.Brine flows through the diaphragm, and the resulting solution contains NaOH, NaCl, and water.
3.Product Separation:
1.The solution is concentrated and purified to remove residual NaCl and water.
●
Advantages:
•Simpler and cheaper than the membrane cell process.
•
Disadvantages:
•NaOH contains impurities like NaCl.
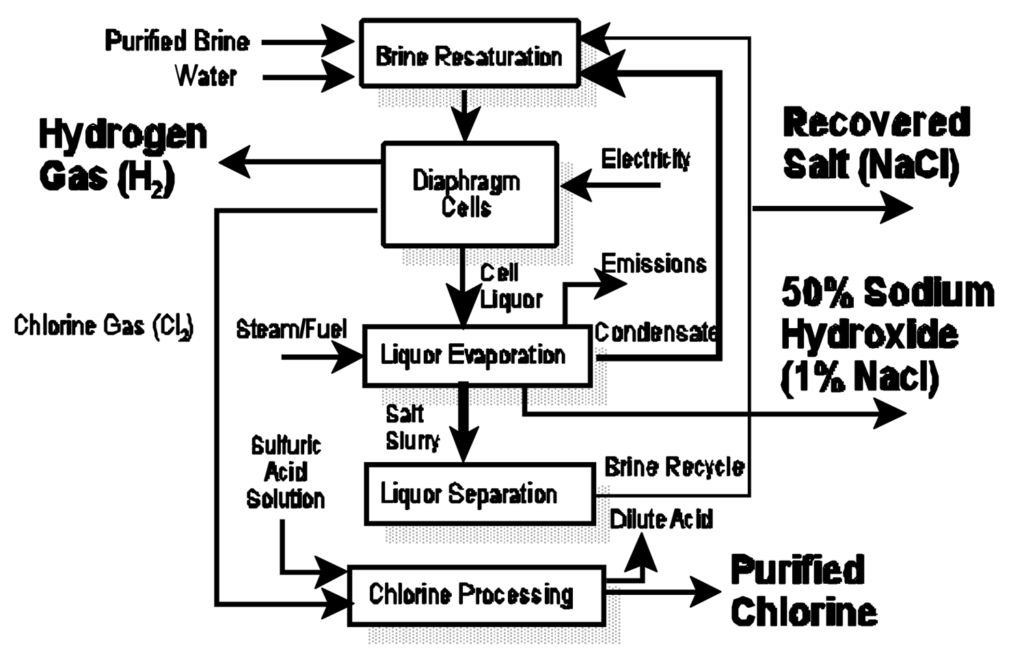
Feature | Diaphragm Cell | Membrane Cell |
Separation Mechanism | Porous diaphragm (partial separation). | Ion-selective membrane (complete separation). |
NaOH Purity | ~10–12%, contaminated with NaCl. | ~30–35%, high purity without NaCl. |
Energy Efficiency | Lower due to ion leakage. | Higher due to selective ion transport. |
Material | Asbestos (old) or PTFE (modern). | Fluorinated polymers (e.g., Nafion). |
Environmental Impact | Moderate (asbestos use in older systems). | Low (no asbestos; more eco-friendly). |
Installation Cost | Lower (simpler design). | Higher (advanced technology). |
Mercury Cell Process
Outdated and Phased Out Due to Environmental Concerns
Steps:
Electrolysis:
1.Mercury acts as the cathode, forming an amalgam with sodium.
2.Chlorine gas is produced at the anode.
3.The sodium amalgam reacts with water in a separate chamber to produce NaOH and hydrogen gas.
2Na(Hg) + 2H2O → 2NaOH + H2 + Hg
Product Recovery:
NaOH and hydrogen gas are separated.
Disadvantages:
Mercury pollution and high energy consumption.
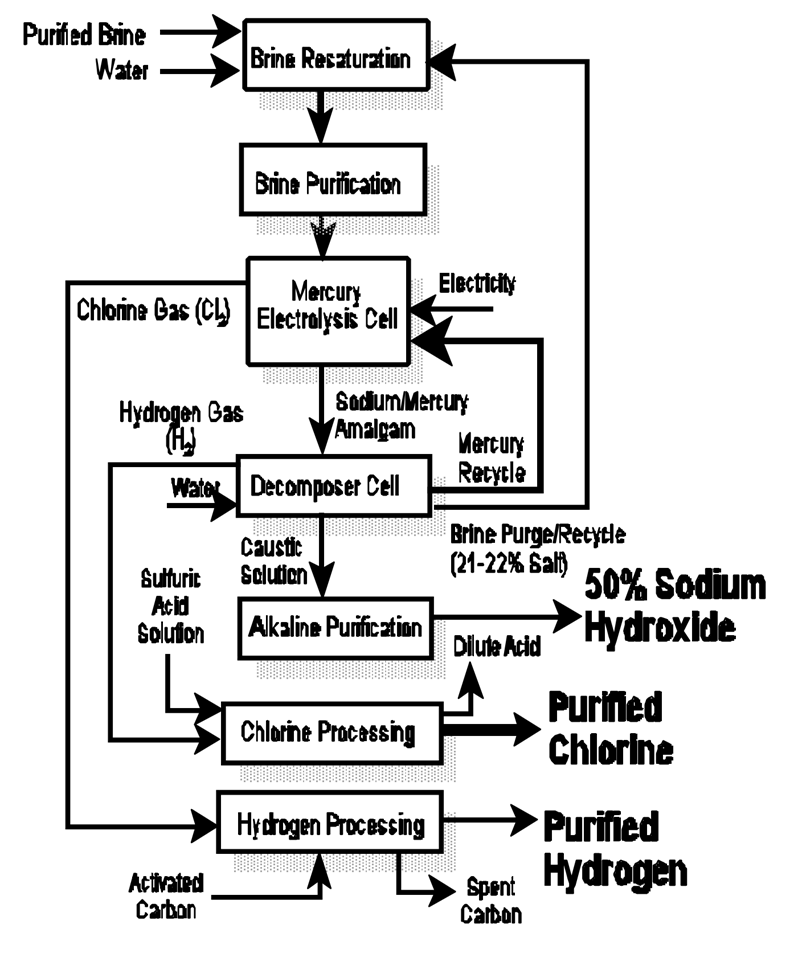
Characteristics of Various Chlorine/Sodium Hydroxide Electrolysis Cells
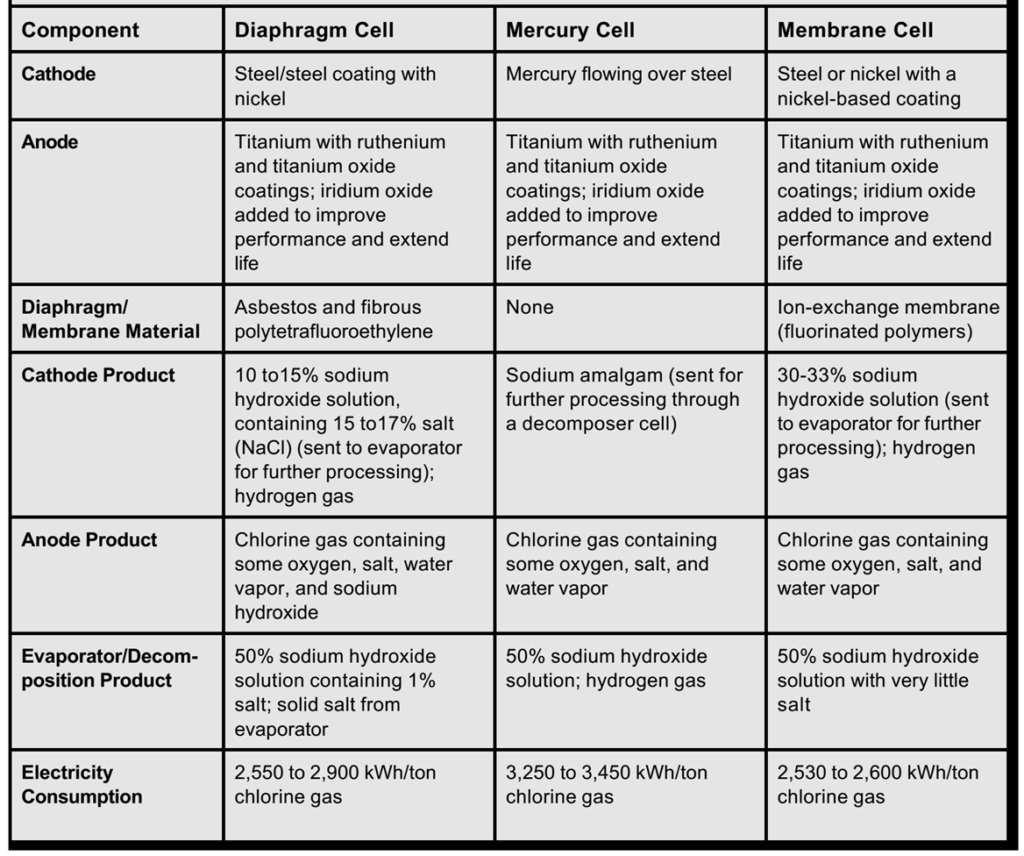
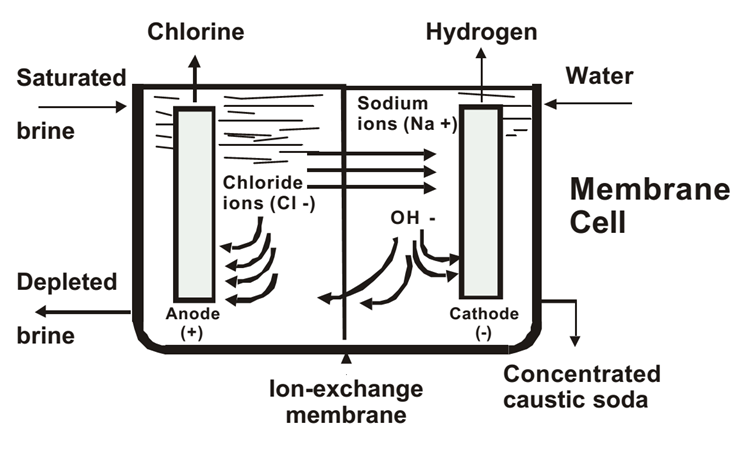
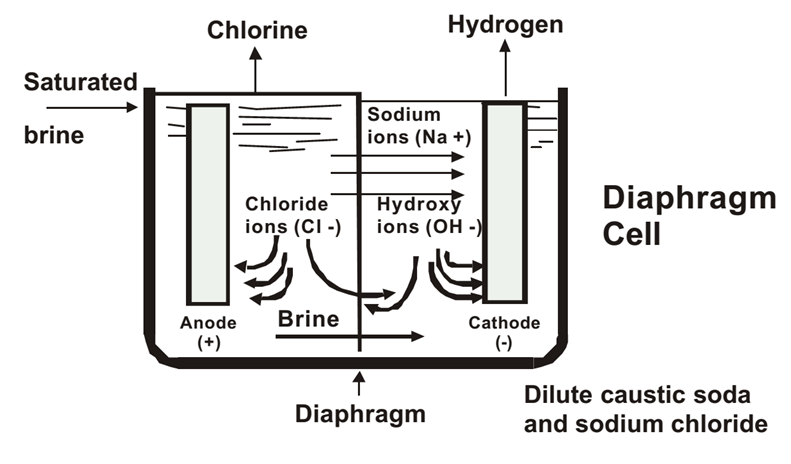
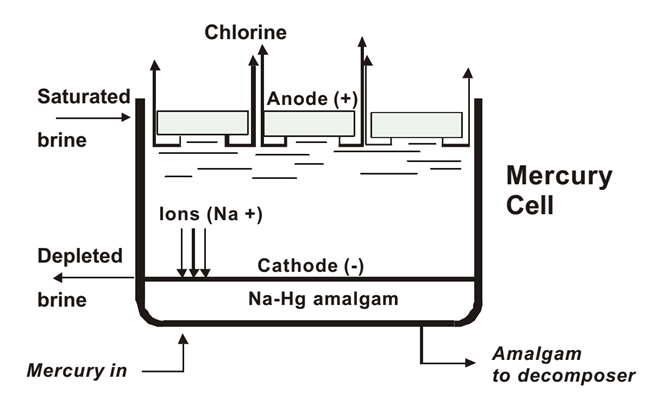
Manufacture of Soda Ash
The manufacture of soda ash (sodium carbonate, Na₂CO₃) is primarily carried out using the Solvay Process, which is the most efficient and widely used method.
Raw Materials:
1.Sodium Chloride (NaCl) – Common salt.
2.Limestone (CaCO₃) – Source of carbon dioxide.
3.Ammonia (NH₃) – Recycled within the process.
4.Water (H₂O) – For solution preparation and reactions.
Overall Reactions:
Formation of sodium bicarbonate:
NaCl + NH3 + CO2 + H2O → NaHCO3 +NH4Cl
Formation of soda ash:
2NaHCO3 → Na2CO3 + CO2 + H2O
Key Steps in the Solvay Process:
1. Brine Purification:
Sodium chloride (brine) is purified to remove impurities like calcium and magnesium.
2. Ammoniation of Brine:
Ammonia gas (NH₃) is bubbled through the purified brine, forming ammoniated brine.
NH3 + H2O → NH4+ + OH−
3. Carbonation:
Carbon dioxide from the calcination of limestone is passed through the ammoniated brine, forming sodium bicarbonate as a precipitate:
•
NaCl + NH3 + CO2 + H2O → NaHCO3 + NH4Cl
4. Filtration:
•Sodium bicarbonate is filtered out of the solution.
5. Calcination of Sodium Bicarbonate:
Sodium bicarbonate is heated to produce soda ash and release carbon dioxide:
2NaHCO3 → Na2CO3 + CO2 + H2O
6. Ammonia Recovery:
Ammonium chloride from the solution is treated with lime (Ca(OH)₂) to regenerate ammonia:
2NH4Cl + Ca(OH)2 → 2NH3 + CaCl2 + 2H2O
The recovered ammonia is recycled into the process.
By-Products: Calcium Chloride is generated during ammonia recovery and usually discarded.
Applications of Soda Ash:
•Glass manufacturing.
•Detergents and soaps.
•Water treatment.
•Chemical synthesis (e.g., sodium bicarbonate).
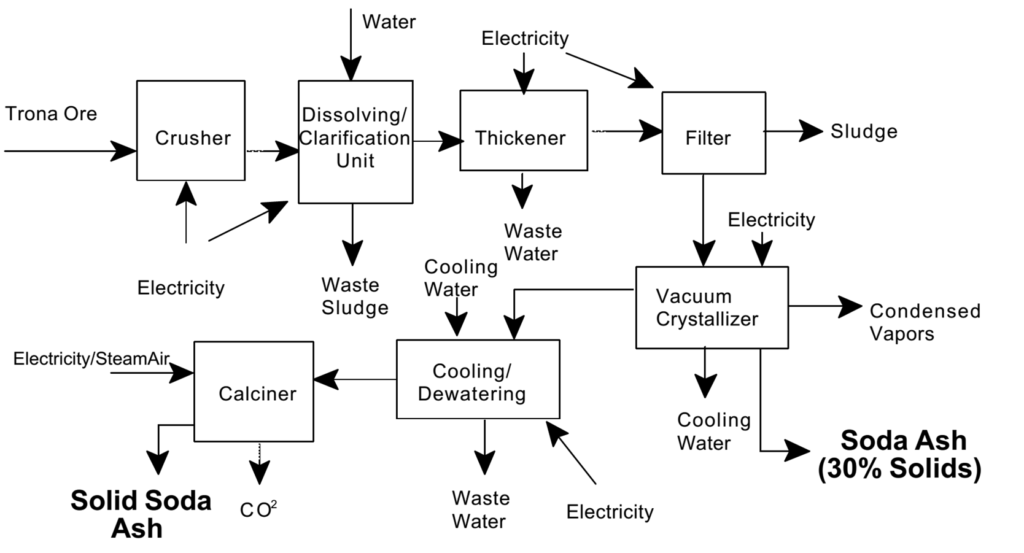